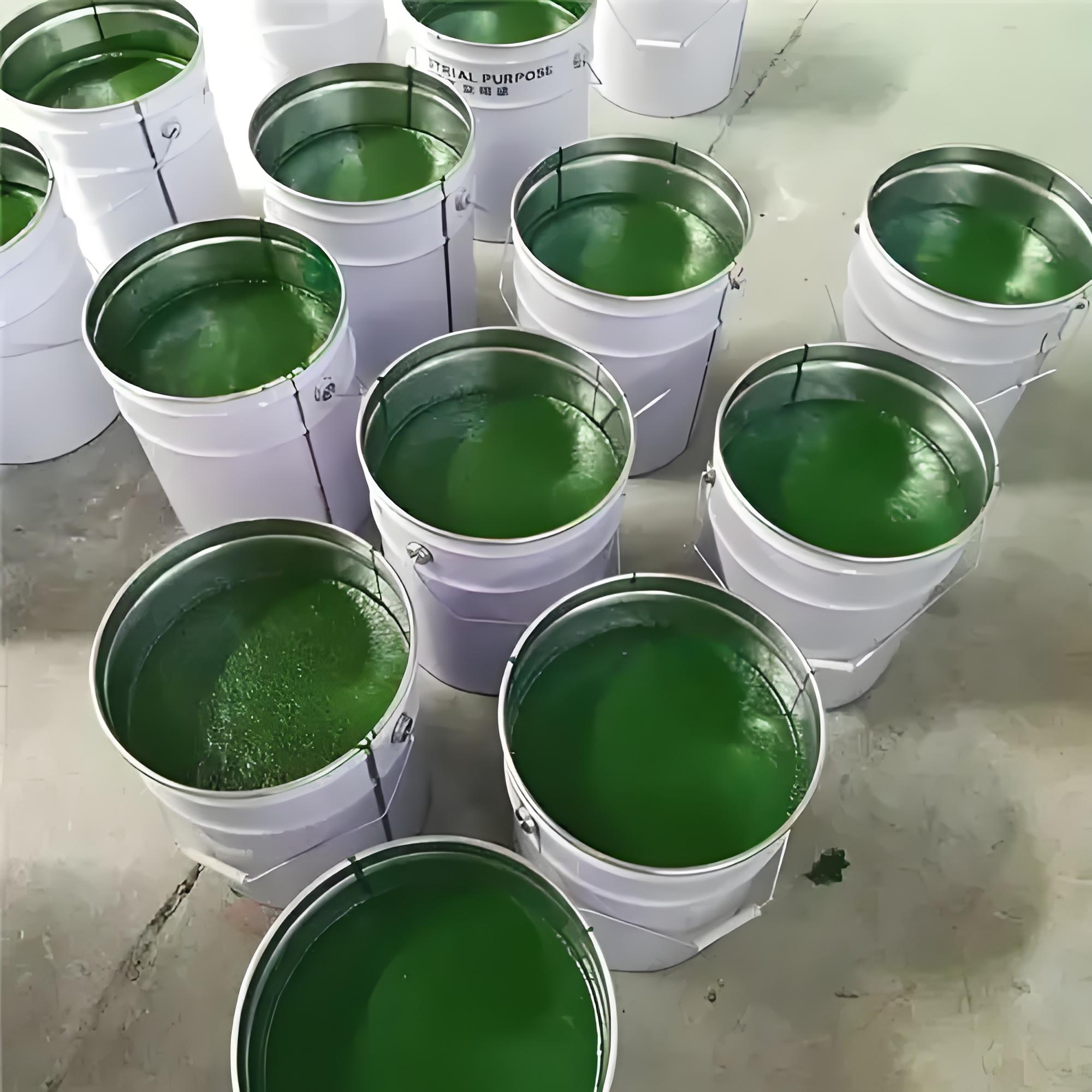
HCPE: The green Pioneer of the anti-corrosion Materials Revolution
High chlorinated polyethylene (HCPE), an environmentally friendly material synthesized through chlorination modification with polyethylene as the main chain, is rewriting the history of anti-corrosion coatings. Compared with traditional chlorinated rubber, its chlorine content is stably maintained at 62%-65%. It not only retains the excellent corrosion resistance of chlorine-based materials but also completely eliminates the carbon tetrachloride solvent through the water phase suspension method, making it a green alternative material that combines environmental protection and performance. From chemical storage tanks to cross-sea Bridges, from extremely cold oil pipelines to cultural relic protection projects, HCPE, with its environmental protection genes, performance breakthroughs and economic advantages, has established a new model for anti-corrosion in modern industry.
In the traditional production process of chlorinated rubber, 0.8 tons of carbon tetrachloride released per ton of product was once a lethal poison to the ozone layer. HCPE, on the other hand, adopts the aqueous suspension method, using water instead of toxic solvents, which directly reduces carbon emissions by 62%, and the solvent residue is only 3.6% of that of chlorinated rubber. This technological innovation not only enabled the factory to get rid of the pungent chemical smell, but also allowed our country to achieve the emission reduction target of the Montreal Convention three years ahead of schedule.
On the oil pipeline of the Qinghai-Tibet Plateau at minus 30℃, the HCPE coating can still be as flexible as rubber. When facing chemical storage tanks with strong acids and alkalis, its corrosion resistance is 30% higher than that of chlorinated rubber. More importantly, a single layer of HCPE coating can achieve a thickness of 120 microns, increasing the construction efficiency by 40%. Data from a large shipyard in 2023 shows that after adopting HCPE coating, the dry-docking repair cycle of ships has been shortened from 45 days to 27 days.
The aqueous phase method for production reduces the cost of HCPE by 25% and does not require expensive waste gas treatment equipment. The breakthrough in modification technology has made it more compatible with epoxy resin systems, and it has played a significant role in the field of cultural relic protection. In the steel structure reinforcement project of the Mogao Caves in Dunhuang, the HCPE coating can not only prevent salt and alkali erosion but also will not release volatile substances that damage the murals.
From the laboratory to super projects, the rise of HCPE attests to the strong vitality of green technology. Currently, the laboratory verification of bio-based HCPE has been completed, and the carbon footprint of the new generation of products made from corn stalks has been further reduced by 50%. This technological revolution that began with environmental protection bans will eventually lead humanity to build an industrial civilization that is both as solid as steel and as pure as water.
Shandong AXA Chem Co.,Ltd
May 14, 2025
Leave a Reply
Your email address will not be published. Required fields are marked *