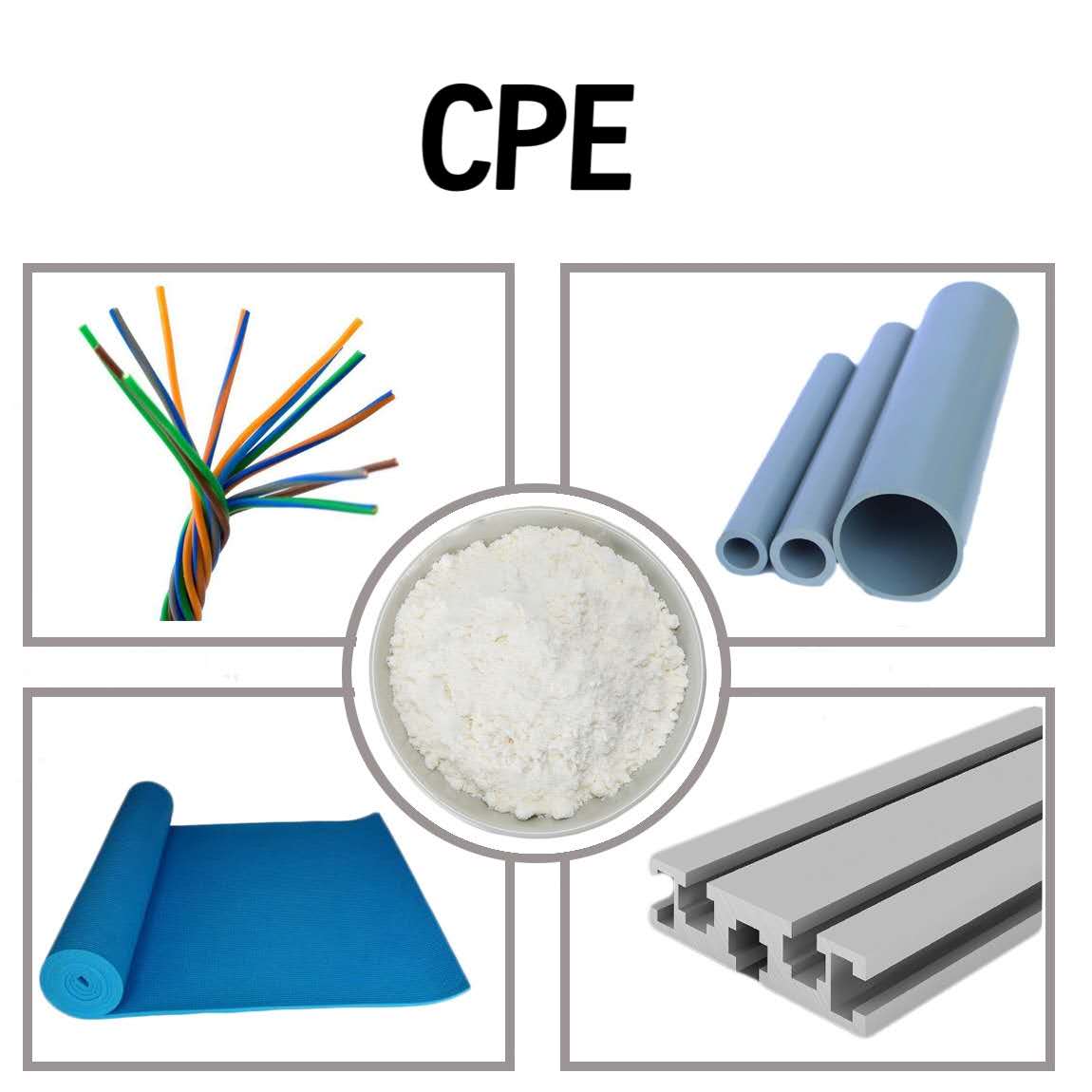
CPE product classification and application area
Chlorinated polyethylene (CPE) is a type of functional polymer material obtained through chlorination modification of polyethylene. Its properties can be flexibly regulated by chlorine content, molecular structure and processing technology, and it is widely used in multiple industrial fields such as plastics, rubber and building materials. According to the differences in chlorine content and material properties, CPE is mainly divided into three categories: resin type, rubber type (CM), and high chlorinated polyethylene (PE-HC).
Among resin-based CPE, type A (with chlorine content ranging from 25% to 40%) is the mainstream in the current market, accounting for over 75% of the total domestic demand. Particularly, its application as an impact modifier in rigid PVC products (such as plastic-steel door and window pipes) accounts for more than 80% Type C (with a chlorine content of 50%-70%) combines the characteristics of both resin and elastomer, and is often used in the blending modification of high-end plastics and the development of flame-retardant materials.
The chlorine content of rubber-type CPE(CM) is 30%-40%. Its elastomer properties enable it to be used alone as a special rubber or blended with ethylene propylene rubber (EPR) and nitrile rubber (NBR) to manufacture oil-resistant rubber hose seals and highly flame-retardant conveyor belts.
As a product with high chlorine content (>40%), the PE-HC type performs outstandingly in fields such as corrosion-resistant coatings and special sealing materials. For example, the acid and alkali resistance of anti-corrosion coatings for chemical equipment can be increased by more than 40%.
From the perspective of application scenarios, the core value of CPE lies in its multi-functional modification capability. In the plastics industry , type A CPE significantly reduces the production cost of window and door profiles and pipes (about 15%-20%) by enhancing the low-temperature toughness and weather resistance of PVC. Meanwhile, when blended with PE and PP, it improves flame retardancy, and when blended with ABS, it enhances aging resistance. In the field of wire and cable , rubber-based CPE (CM) has become the preferred material for mine cable sheaths and control cable insulation due to its oil resistance and heat resistance (meeting UL94 V0 flame retardancy standard), while resin-based CPE has shown excellent UV resistance in the outer protection of 5G cables. Youdaoplaceholder0 Building materials is another important direction. Waterproofing membranes made by blending CPE and PVC have 30% better weather resistance, are suitable for high temperature and high humidity environments, and cost 18% less than traditional materials; The PE-HC type is used to develop long-lasting anti-corrosion coatings, covering harsh scenarios such as chemical pipelines and Marine facilities.
In the future, the CPE industry will develop in depth towards high performance and intelligence. Nanocomposite technology can reduce the addition amount of flame retardant to less than 30% while maintaining the material strength > 15MPa. Trials of CPe-based conductive composites have begun in the fields of flexible electronics and smart wearables, with their electrical conductivity improved by 40%. As global attention to sustainable materials heats up, CPE, with its customizable advantage, is expected to have a market share of over 65% by 2025, becoming a key growth point in the polymer materials field.
Shandong AXA Chem Co.,Ltd
May 6, 2025
Leave a Reply
Your email address will not be published. Required fields are marked *